各工程の設備データを「SensorCorpus」に収集し検査結果と照合することで、不具合の早期特定と原因究明が可能なシステム基盤を構築。
これにより、製造現場と品質保証部門間でリアルタイムなデータ共有が実現され、改善サイクルの高速化され製品歩留まりの大幅な向上しました。
課題
- 発生した問題の分析に必要なデータの収集の時間の削減。
- 品質管理をするために必要なデータが製造現場と品質保証部間を共有できるようにする。
解決策
- 不具合箇所・原因の特定が早期に可能なシステム基盤を構築。
- 各製造工程に設備の電圧、電流、回転数、溶液濃度等の様々なデータを「SensorCorpus」に格納。
- データと検査工程における検査機からの結果とを突合させることにより、どの工程で不具合が発生したか、場所および原因の特定を行えるようにした。
- 品質チェック作業にAIを活用・自動化させることで作業効率化を図った。
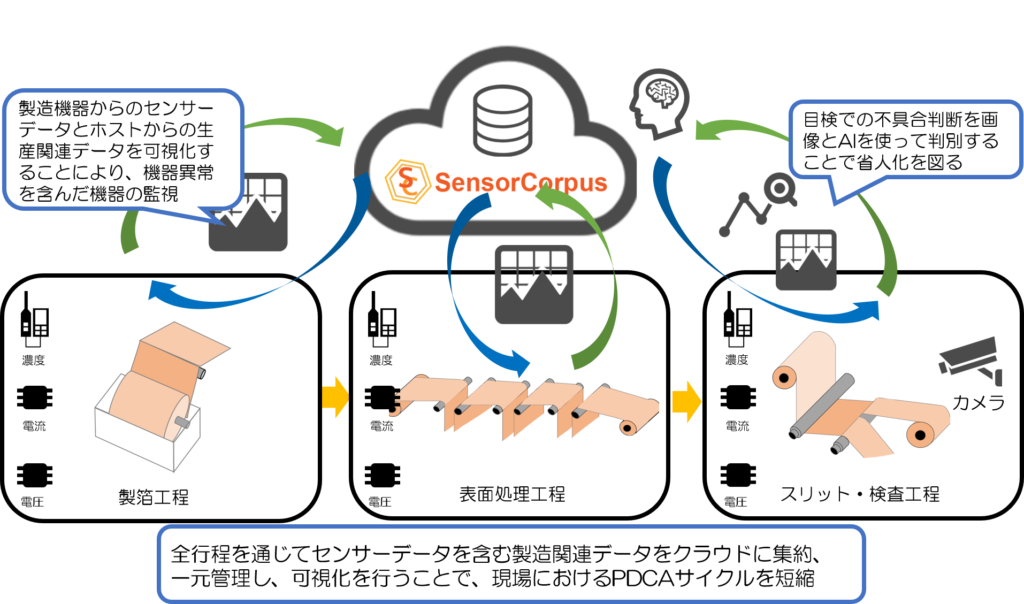
結果
- 社内部門間で品質判断に必要なデータをリアルタイムに共有できるようになり、製品歩留まりの大幅な向上。
- 各製造工程のデータと検査工程における検査機からの結果と突合させることが容易になり、不具合箇所および原因の特定時間の削減。
- 問題の早期発見、共有が可能なため、改善PDCAの高速化を実現。
今後
- AIによる自動化を行うための学習を行い、更なる作業効率向上を目指す。
◎使用センサー
- 電流センサー
- 電圧センサー
- 濃度センサー
- 回転センサー
- 画像検査機